Laser micromachining
Laser micromachining includes processes requiring perfect quality and extreme precision: fine laser cutting, laser drilling, 3D laser micro-engraving, laser surface texturing, laser micro-welding, laser marking, surface preparation, etc.
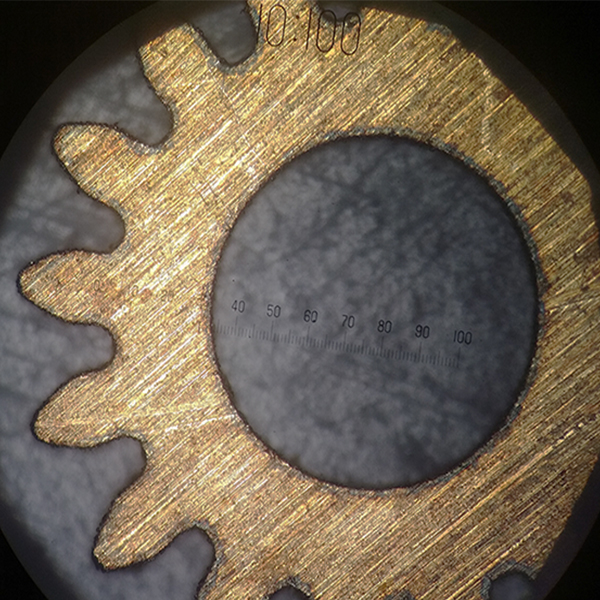
Laser cutting
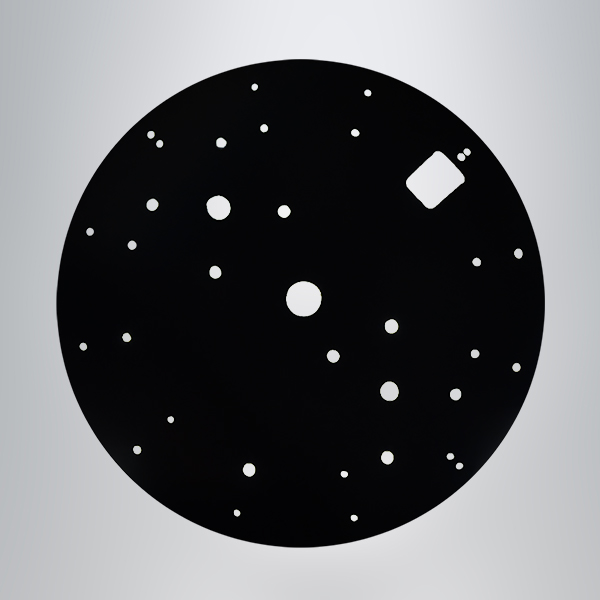
Laser drilling
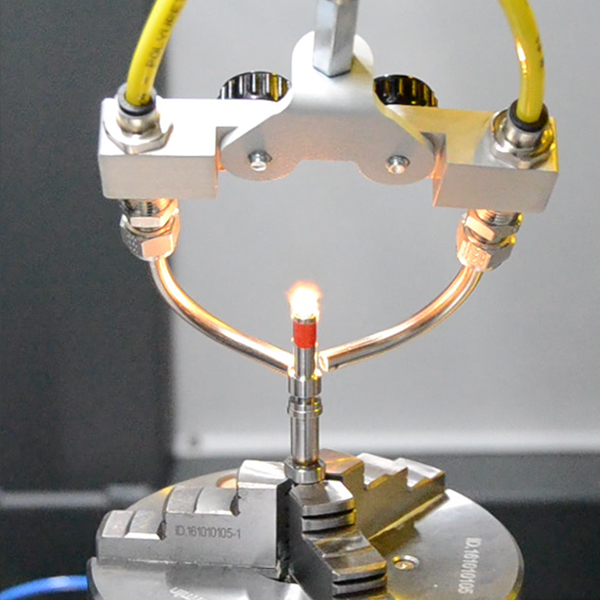
3D micro-welding
Lasers Micromachining techniques
Laser micro-welding
The laser welding technique ensures the production of micrometric welds with outstanding mechanical properties that competition those of the base material. The specific features of industrial laser welding (high energy density, finesse and precision) also ensure high welding speed, aesthetic spot or seam welds and exemplary reliability. As a non-contact process, laser welding meets the expectations of the most complex assembly projects, allowing even welds that are impossible to obtain using conventional techniques.
Materials
Metals – Precious metals – Aluminium – Iron – …
- Very high precision
- Perfect repeatability
- High welding speed
- With or without filler material
- No contamination
- Excellent finesse
- Minimal or no deformation
- Robust and watertight welds
- Simple or complex geometries
- Environmentally friendly process
Laser micro-engraving
Laser engraving (2.5D or 3D) – are the main techniques for decorating parts with high added value, where aesthetics and quality of finish are essentials. The laser machines manufactured by our teams can decorate both flat parts and complex surfaces (tilted, conical, cylindrical) and on many materials, including precious metals (gold, silver, platinum, synthetic diamonds, zirconium and aluminium oxides, etc.).
Materials
Metals – Precious metals – Aluminium – Iron – …
- Unique decoration
- Micrometric accuracy
- Exceptional rendering
- Economical processes (no consumables)
- Inimitable process
- High level of detail
- Small to large series of parts
- Unbreakable decoration
Laser micro-cutting
Laser cutting is a non-contact, high precision thermal separation process. On the surface of the material, the high-energy laser beam causes the material to melt, evaporate and sublimate, ensuring narrow and aesthetic cutting edges. The high quality of the cut as well as the performance of the process (speed, positioning tolerances, etc.) are determined and adapted for each project by the choice of several criteria: the laser source and parameters, the focusing optics, the assist gas, etc.
Materials
Metals – Precious metals – Aluminium – Iron – …
- Extreme precision
- Clean and aesthetic edges
- Negligible mechanical deformation
- Minimum thermal stresses
- Perfect reproducibility
- High speed of machining
- Non-contact method
- Material saving
Laser micro-drilling
Laser drilling allows the creation of holes (through or blind) with regular contours and micrometric sizes on all materials, including precious metals. The laser beam – specially shaped and concentrated to obtain a very high power density – will melt, then evaporate and sublimate the part to be drilled. The quality of the contours and the speed of the process (up to several thousand holes per second) are ensured by the specific features of the laser and by the almost instantaneous expulsion of the molten material from the hole, caused by the shock wave and the use of an assist gas.
Materials
Metals – Precious metals – Aluminium – Iron – …
- Micrometric precision
- High reliability
- Fast process
- Minimum requirements for materials
- Material saving
- Fine and aesthetic contours
- Simple or complex forms
- Reduced heat-affected areas
- Simple tools
Laser texturing
Laser texturing is a process that transforms the surface condition of a material by changing its texture. It is also a technique used for laser decoration. Laser texturing is also used for the surface preparation of a coating. ES LASER laser machines can be used to perform laser texturing on 3D parts in many fields of activity (automotive, tyres, packaging, cosmetics, luxury goods, medical, etc.)
- Accuracy
- Versatility
- Original textures
- Reduction of environmental impact
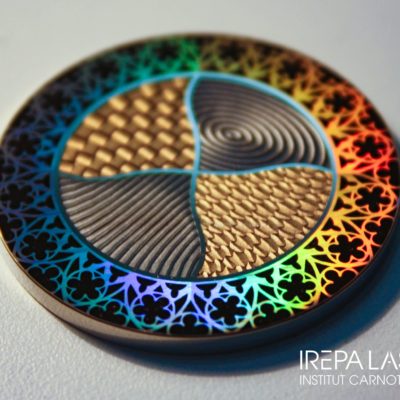